Manual Flushing Method – A Hands-On Approach to Material Consumption in MS D365 Business Central
- akash shukla
- Feb 26
- 2 min read
Updated: Feb 26
In the world of manufacturing and production, managing material consumption efficiently is critical to maintaining accurate inventory records and ensuring smooth operations. One of the key methods to achieve this in Business Central is the Manual Flushing Method. This method provides precise control over material consumption by requiring manual entry of consumption data. Let’s explore how this method works, its applications, and how to implement it effectively.
What is the Manual Flushing Method?
The Manual Flushing Method is a process where material consumption is recorded manually in the system. Unlike automated methods, this approach requires users to enter consumption details in the Consumption Journal or Production Journal. It is particularly useful when production processes are complex, or when materials need to be tracked with high precision.
How Does Manual Flushing Work?
Here’s a step-by-step guide to implementing the Manual Flushing Method:
Set the Flushing Method on the Item Card:
Navigate to the Items List and select the item you want to configure.
Open the Item Card and go to the Replenishment FastTab.
In the Flushing Method field, select Manual.
Create a Released Production Order:
Create a production order for the finished good (e.g., a Sofa).
Refresh the production order. The flushing method from the item card will be copied to the production order components.
Post Material Consumption Manually:
Go to the Consumption Journal or Production Journal.
Use the Calc. Consumption button to automatically populate the journal lines with the required components and quantities.
Review the entries, add any additional details (e.g., dimensions, bin codes, or serial/lot numbers), and post the journal.
Verify Consumption in Item Ledger Entries:
Open the released production order and navigate to Item Ledger Entries to confirm that the consumption has been recorded accurately.
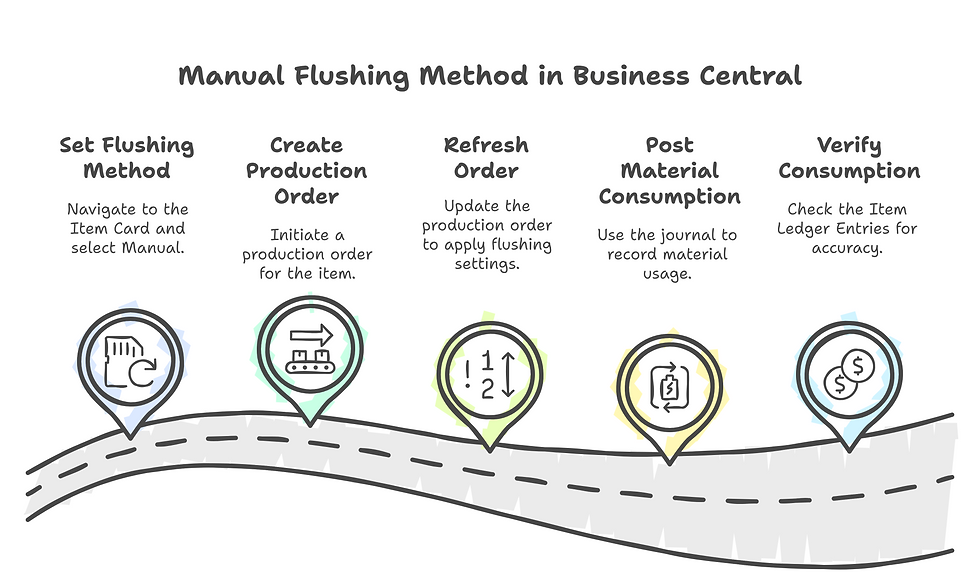
Practical Example
Imagine a company producing custom furniture. Each piece of furniture requires unique materials, such as specific types of wood or upholstery. Using the Manual Flushing Method:
The production team creates a released production order for a custom sofa.
They manually enter the consumption of materials like fabric, foam, and wood in the Consumption Journal.
After posting, the system updates the inventory records, ensuring accurate tracking of materials.

Advantages of Manual Flushing
Precision: Allows for detailed tracking of material usage.
Flexibility: Suitable for custom or non-standard production processes.
Control: Provides full oversight over material consumption.

Tips for Effective Manual Flushing
Always double-check entries in the Consumption Journal to avoid errors.
Use dimensions, bin codes, or serial/lot numbers for additional tracking if needed.
Regularly review Item Ledger Entries to ensure accuracy.
Comments