Simplifying Material Consumption with the Backward Flushing Method in D365 Business Central
- akash shukla
- Mar 13
- 3 min read
In manufacturing, balancing efficiency and accuracy is a constant challenge. The Backward Flushing Method in Business Central provides a streamlined solution by automating the recording of material consumption at the end of the production process.
This method is especially beneficial for industries with predictable material usage and standardized workflows.
Let’s break down how Backward Flushing works, where it’s most useful, and how to implement it effectively.
What is the Backward Flushing Method?
The Backward Flushing Method operates on a simple principle: it assumes that all materials are consumed at the start of the production process, but the actual deduction from inventory happens only when the production order is marked as Finished.
This approach is ideal for industries where material usage is consistent and predictable, such as food processing or high-volume manufacturing.
For example, imagine a bakery producing hundreds of loaves of bread daily. Instead of manually tracking how much flour, sugar, and yeast are used for each batch, the bakery can rely on Backward Flushing. Once the bread is baked and the batch is completed, the system automatically deducts the exact amount of ingredients used, saving time and reducing errors.

Here’s a step-by-step guide to implementing the Backward Flushing Method:
1. Set Up the Flushing Method on the Item Card
Go to the Items List and select the item you want to configure.
Open the Item Card and navigate to the Replenishment FastTab.
In the Flushing Method field, select Backward.
2. Backward Flush the Entire Order
Create a Released Production Order and refresh it. The system will copy the flushing method from the item card to the production order components.
Once all operations are completed, change the status of the production order from Released to Finished. The system will automatically post the consumption of materials.
3. Backward Flush by Operation
Assign Routing Link Codes to each operation in the Routing Master and corresponding components in the Production BOM.
As each operation is completed, the system will automatically deduct the materials associated with that operation.
4. Verify Consumption in Item Ledger Entries
After completing the production order, check the Item Ledger Entries to ensure that material consumption has been recorded accurately.
When Should You Use Backward Flushing?
This method is particularly effective in:
High-volume production environments where processes are standardized and repetitive.
Industries with predictable material usage, such as food and beverage, pharmaceuticals, or automotive manufacturing.
Scenarios where raw materials are consumed in fixed proportions, like mixing ingredients in a recipe or assembling components in a factory.
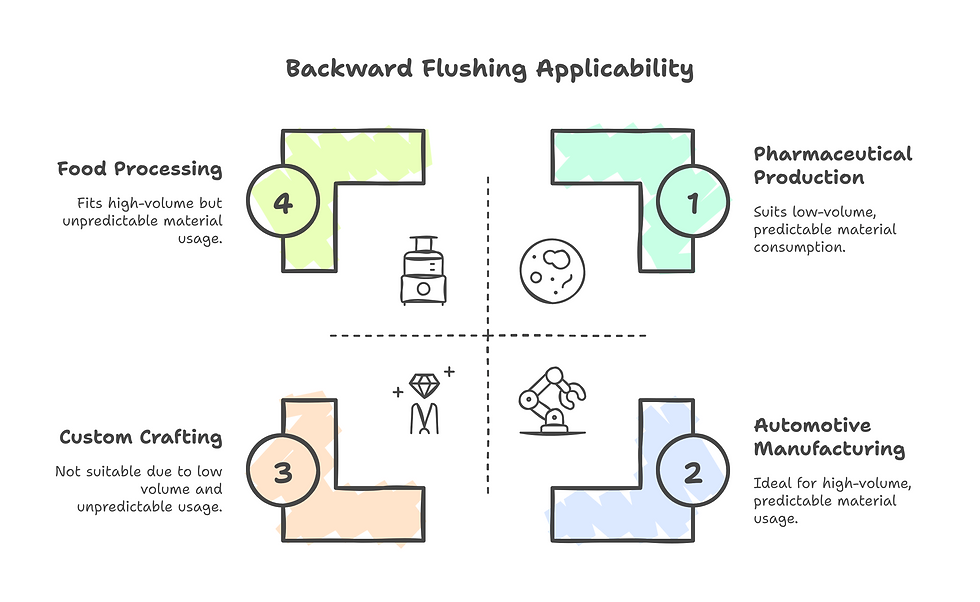
Practical Example: Bottled Beverage Production
Let’s say a company produces bottled beverages. Here’s how Backward Flushing simplifies their process:
The production team creates a Released Production Order for a batch of soda.
Once the batch is completed and the status is changed to Finished, the system automatically deducts the raw materials (e.g., water, syrup, and bottles) from inventory.
This eliminates the need for manual tracking and ensures accurate material usage records.
Advantages of Backward Flushing
Simplicity: Reduces manual effort by automating material consumption at the end of the process.
Consistency: Ensures accurate tracking of materials in standardized workflows.
Efficiency: Perfect for high-volume production environments where time and accuracy are critical.

Informative...Akash Bhai